Features of using T-FLEX CAD for design of large assemblies at BorMash LLC
Author: Alexander Medvedev, design engineer of BorMash; Polina Goncharova, marketing specialist of Top Systems
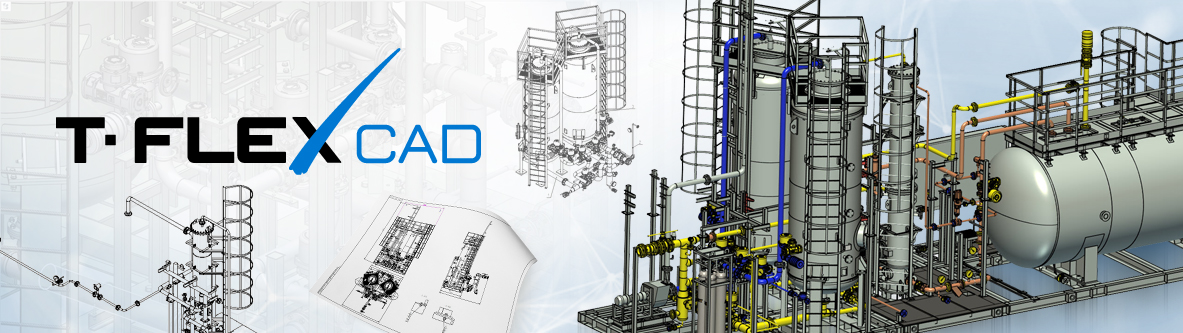
Results of 3D modeling and engineering projects competition "CAD Competence 2021" have already been summed up. Undoubtedly, a most memorable project that won the "Expert" nomination was an assembly model of a carbon-vacuum adsorption vapor recovery unit of the UUVA-02-D type (Fig.1,2). Containing more than 18,000 bodies, the model is characterized by a high degree of detail, and based on it, a real operating unit was created and mounted. The project is fully built in T-FLEX CAD using key features of the system. For this reason, we asked the author of the project, Alexander Sergeevich Medvedev, a design engineer at BorMash LLC, to tell us in more detail about operation of the unit, as well as about the assembly design process in T-FLEX CAD.
BorMash LLC is a modern, dynamically developing enterprise, whose main activity is design, production, supervision installation and maintenance of air cooling devices, shell-and-tube heat exchangers, capacitive, column and filtration equipment.
Fig. 1 – Model of a vapor recovery unit
Fig. 2 – Model of a vapor recovery unit (top view)
Principle of operation of the vapor recovery unit
This project appeared as an order of one of oil refineries in Russia. The unit, designed for recovery of vapors in production of automobile gasoline, reduces loss of petroleum products, as well as emissions of harmful substances (Fig. 3).
Fig. 3 - General view of the platform with columns, stairs and service platforms with overall dimensions.
It consists of a horizontal steel tank, adsorbers, an absorption column, a piping arrangement of these devices (Fig. 4), shut-off and control valves, automated control and instrumentation devices (Fig. 5).
Fig. 4 - Piping arrangement of columns with stairs and service platforms. An isometric projection is shown for the sake of clarity and for better understanding of the design of the device.
Fig. 5 - Fragment of the piping arrangement of the unit with elements of shut-off and control valves, ball valve actuators, instrumentation and control devices.
The point of this VRU, working on adsorption technology, is pick-up of hydrocarbon vapors (adsorbate) formed during storage and transportation on the surface of solid sorbents (adsorbent). As a rule, activated carbon is used as an adsorbent for hydrocarbons.
Since an air-vapor mixture (a mixture of air and hydrocarbon vapors) always occurs during storage and transportation of hydrocarbons, the initial task of the adsorption-type VRU is to separate air and hydrocarbon vapors. This happens in containers filled with activated carbon. Most often, a pair of filters is used in the VRU for sequential operation – one in absorption mode, the second in regeneration mode.
When the gas-air mixture flows from bottom to top through the container with coal, hydrocarbons are absorbed on the surface of the coal. At this time, part of the clean air is filtered and goes through pipeline into the atmosphere.
Activated carbon is saturated with hydrocarbons to a certain level, and then the filter with saturated hydrocarbon vapors is switched to the regeneration mode. The absorption of hydrocarbon vapors entering the VRU continues with the help of a second container with coal.
Coal regeneration is carried out by vacuum, which is created in the VRU system with the help of different types of vacuum pumps. When coal is regenerated in a coal filter by means of a vacuum system (Fig.6) already concentrated hydrocarbon vapors released from the surface of the adsorbent are transferred to the absorption column. In the column, hydrocarbon vapors are irrigated by oncoming flow of fresh absorbent (automobile gasoline), absorbed by it and diverted to an absorbent collection tank.
Fig. 6 - Platform with an absorber and a vacuum pump designed for regeneration of activated carbon and transfer of hydrocarbon vapors into the absorption column.
Design process
During development of this model, all the advantages of the T-FLEX CAD system were fully used, and parametric capabilities of the system turned out to be the most significant for the project (Fig.7).
Fig. 7 - 3D model of a flange modified by specialists of BorMash LLC taking into account diameters of connecting pipelines and a type of weld, depending on a nominal inside diameter of the flange.
With the help of parameterization, the company was able to develop all the design documentation necessary for production, as well as manufacture this equipment in a very short time. From the start of work to the handover of working construction documents to production, a little more than 1.5 months passed (Fig.8). It became possible to develop the project so quickly mainly due to the flexible functionality of T-FLEX CAD, which allows you to customize the system to specific needs of each user. So, in terms of parameterization, there were almost no restrictions.
Fig. 8 - Photos of the unit mounted according a 3D model
All assembly units have a complete set of detailed drawings and BOM for production (Fig.9). A feature of this project is a complete 3D model of the unit with all parts and nodes with maximum detail, including instrumentation and control devices (Fig.10).
Fig. 9 - Modified prototype of the BOM taking into account requirements of the document management system at BorMash LLC.
3D models of bought-out components were requested from suppliers or were created independently based on real products. The library of materials and standard products of T-FLEX CAD was fully used. In addition, parts and prototypes needed at the enterprise were created on the basis of standard products.
Fig. 10 – In-depth development of the 3D model of the unit.
Fig. 11 – In-depth development of the 3D model of the unit.
This type of equipment was manufactured at BorMash LLC for the first time, despite more than 20 years of company experience in production of equipment for oil and gas processing and mining, chemical, metallurgical, energy industries.
It is very important for Top Systems that the T-FLEX CAD system helped experienced employees of the enterprise to complete the project in the shortest possible time! We wish BorMash successful projects and hope for further cooperation.